As any engineer knows, time is a critical resource. Nothing is more frustrating than being stuck in a cycle of waiting. For those working with SolidWorks on large assemblies, the pain is all too familiar. Frequent crashes, slow loading times, and the sheer size of files can grind your productivity to a halt. The situation has become so dire that many engineers have resorted to using two workstations—one to work on smaller tasks while the other struggles to open a large assembly. This issue is so common that part of our consulting work is to help engineers resolve these types of problems (case in point, see this video). However, this is hardly a sustainable solution. Let’s explore better ways to resolve a slow SolidWorks environment.
The Engineering Pain: SolidWorks Slowdowns and Workarounds
The complexity of designs is increasing, and with it, so are the file sizes in CAD applications like SolidWorks. This growth in complexity often leads to slowdowns that cripple an engineer’s ability to work efficiently. When opening a large assembly can take upwards of 30 minutes—or worse, cause your system to crash—every task becomes a battle against time.
This problem is exacerbated by the fact that SolidWorks, while powerful, was not designed to handle massive assemblies. However, these assemblies and other intricate designs are now commonplace in many industries. For example, SPK has one client in the aerospace industry that has an assembly of an entire plane. As a result, engineers are left waiting, unable to make progress on their projects. This leads to missed deadlines and mounting frustration.
The Solutions: Exploring Better Tools and Strategies
Fortunately, there are solutions to these issues, helping engineers to reclaim their productivity and reduce downtime. Here are three approaches to overcoming the SolidWorks slowdown problem.
Creo: An On-Premises Powerhouse
For those who are deeply embedded in on-premises workflows, PTC’s Creo offers a powerful alternative to SolidWorks. Creo is designed to handle the complexities of large assemblies with greater efficiency, thanks to its robust underlying engine. Unlike SolidWorks, Creo manages memory more effectively. This significantly reduces the risk of crashes and slowdowns.
The differences in the engines behind Creo and SolidWorks are significant. Creo’s architecture is optimized for performance on large-scale projects, making it a go-to solution for engineers who need reliable performance. By switching to Creo, engineers can experience faster load times, fewer crashes, and a more stable working environment. SPK’s clients have benefited from our CAD migration services. We provide consulting services to determine the right approach and proper steps. Coupled with SPK’s hosted Windchill PLM solutions, clients help modernize their solutions and provide the foundation for innovation.
Creo+: The Future of CAD in the Cloud
For teams looking to leverage the power of the cloud, PTC’s Creo+ is the next evolution of CAD tools. As a SaaS offering, Creo+ combines the performance of Creo with the flexibility of cloud-based access. This means you can work on your designs from anywhere, without being tied down to a specific workstation.
While Creo+ offers the robust performance engineers need for large assemblies, it also has additional benefits. One of its main capabilities is using cloud resources to handle complex calculations and data storage. This reduces the burden on your local machine and ensures that your work is always backed up and accessible. For teams spread across multiple locations, the collaborative features of Creo+ make it easier to work together without the typical bottlenecks associated with traditional CAD software. Learn more about Creo+ in one of our recent blog posts where we answer many of the frequently asked questions.
SPK vCAD: Accelerating Productivity
While switching to a different CAD tool might be the ultimate solution for some, others may need to stick with SolidWorks due to legacy projects or company preferences. For these situations, SPK’s vCAD solution can provide a significant boost in performance.
SPK vCAD allows engineers to tap into high-performance computing resources. By offloading the heavy lifting to powerful servers, vCAD can reduce load times and make working with large assemblies more manageable. While it doesn’t address the inherent limitations of SolidWorks, it can drastically improve the overall speed and responsiveness. This allows engineers to get more done in less time. Additionally, it significantly speeds up the use of your Solidworks environment by adding 2x or 10x more CPU, GPU, and memory. Plus, on average, engineers only use their CAD tool for 25 hours. This means IT departments are paying more for the use of those high-performance computers for less than 40 hours per week’s worth of work.
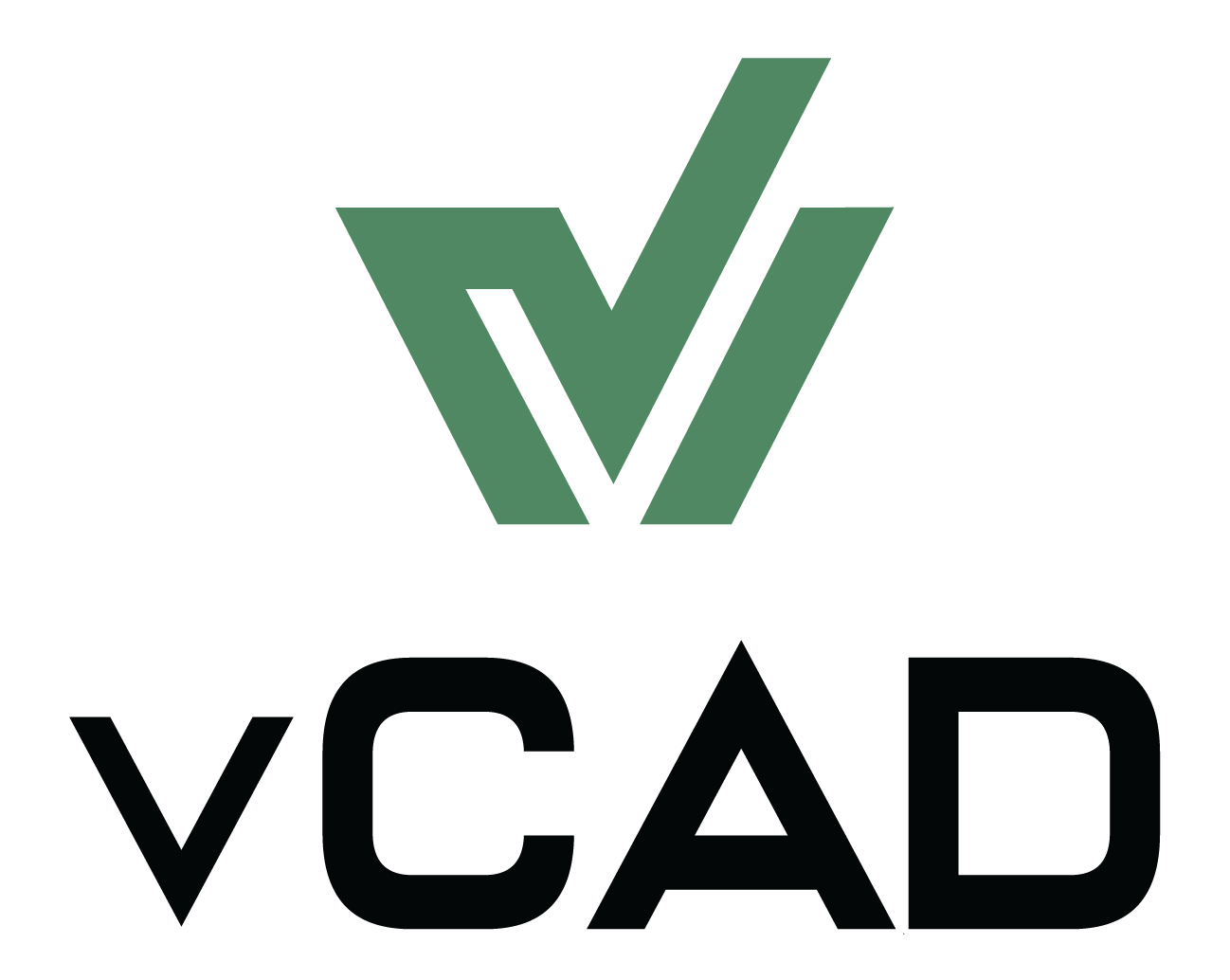
Choosing the Right Path Forward to Eliminate SolidWorks Slowdowns
The frustrations of dealing with SolidWorks slowdowns on large assemblies are real, but they don’t have to be permanent. Whether it’s switching to a more robust tool like Creo, adopting the cloud-based power of Creo+, or supercharging your current setup with SPK vCAD, there are viable paths forward that can help engineers overcome these challenges.
If you’re tired of waiting on your applications and want to explore how these solutions can enhance your productivity, contact SPK and Associates today. Our team can help you find the right tools and strategies to keep your projects on track and your frustration levels low. Don’t let slowdowns hold you back—take control of your productivity with SPK and Associates.