The manufacturing industry is getting more competitive, with engineers expected to deliver the most efficient, cost-effective designs. Meeting the high standards of the industry and client specifications is only possible with the proper tools. PTC’s CAD solution, Creo, offers parametric capabilities allowing engineers to achieve these expectations. Let’s explore how Creo can streamline every stage of machine design.
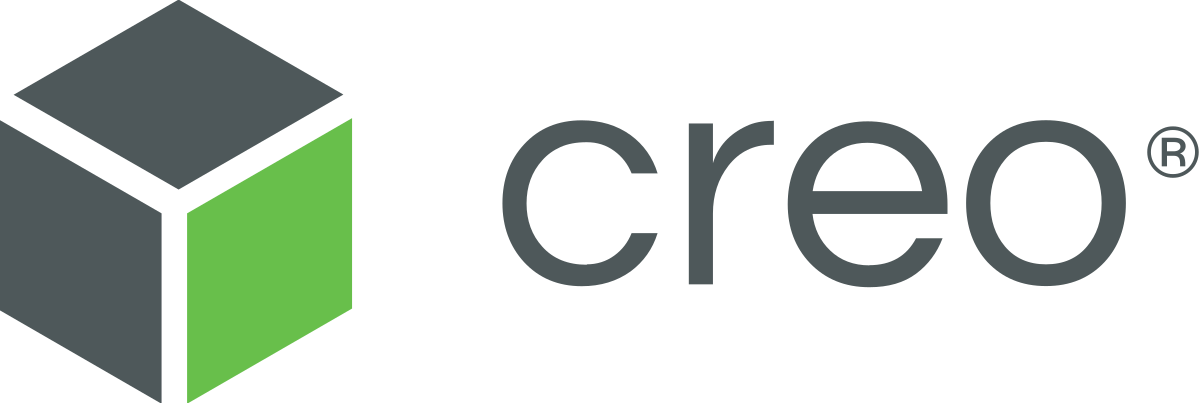
Parametric Capabilities
In CAD software, a parametric capability is any feature that enables designers to adjust models by modifying specific parameters. For example, users can modify dimensions, constraints, or relationships. Once these changes are made, the entire design automatically updates based on these parameters. This makes it quick and easy to make changes as there is no need to recreate or redraw models. Parametric capabilities allow engineers to easily streamline design changes, create multiple product variants, and ensure consistency. No matter what industry your machine is designed for, PTC Creo offers engineers the tools needed to streamline every stage of machine design.
Creo’s Parametric Capabilities for Machine Design
Creo Parametric offers robust 3D modeling capabilities that support iterative design, customization, and rapid prototyping. In addition to this, users can build upon Creo’s already expansive range of features with advanced tools. These include additive manufacturing, model-based definition (MBD), generative design, augmented reality (AR), and smart connected design. These capabilities allow users to optimize the machine design process by integrating design, analysis, and manufacturing in one cohesive platform.
Enhancing Machine Design with Creo
Machine design involves multiple stages, from the initial concept to a production-ready model. Each phase demands specific tools and techniques, and Creo’s parametric capabilities offer the continuous innovation needed throughout the design process.
Concept Design
The first phase in the machine design process is concept design. During this stage, engineers define the layout, configuration, and specifications to achieve a functional machine. Early design decisions are critical for a successful product, especially for specialty machines that handle tasks such as packaging, sorting, or assembly. A solid concept also reduces the risk of lost market share, dissatisfied customers, and wasted resources Using Creo’s design exploration and flexible modeling tools, engineers can quickly create, refine, and assess multiple design alternatives. Creo also offers generative design capabilities that automatically generate optimized design options based on user-defined goals and constraints. This allows for fast iterations, enabling teams to select the best concept before moving into detailed design.
Detailed Design
Once the concept is finalized, users can move on to their detailed design. Creo’s parametric capabilities shine in this phase as engineers and designers document every aspect of the product. Creo’s advanced assembly features allow for seamless management of large, intricate assemblies. It enables concurrent engineering which saves time and top-down design which ensures a stable base to work from. Whether you are working with standard components or a complex configuration, Creo ensures all requirements are adhered to and all components are installed safely. Furthermore, tools like behavioral modeling and Creo Simulation Live support decision-making during the detailed design stage. Lastly, this stage ensures all Product Manufacturing Information (PMI) is accurate before moving to the next step.
Simulation and Analysis
After the detailed design is made, users can move on to simulation and analysis. For specialty machines, performance and durability are paramount. Creo’s robust simulation tools, such as kinematic and dynamic analysis, provide insights into how the machine will operate under various conditions. This allows engineers to test for potential issues in a virtual environment. Additionally, Creo offers simulation-driven design which uses real-time analysis to validate and optimize design decisions. Its real-time simulation allows users to test and validate designs as they are created, and its AR design can be shared to improve stakeholder engagement. Simulations help assess durability, quality, and more critical factors for high-performance machines. By using real-time simulation, designers can continuously evaluate product performance and achieve optimal configurations before moving to manufacturing.
Design to Manufacturing with Creo
For machine designers, moving seamlessly from CAD design to production is vital. Creo provides integrated manufacturing tools, eliminating the need for disconnected solutions or third-party tools. Creo’s additive manufacturing capability allows for direct 3D printer connectivity and optimized print tray setups to easily create parts. Designers can also create custom components or adapt stock items to meet specific requirements. Creo’s mold and tool design capabilities allow users to create specialized tools, molds, or dies to shape materials into desired parts. Lastly, Creo’s ability to support high-speed precision machining and automated tooling enables machine designers to reduce costs, enhance quality, and accelerate the time to market.
Using Creo for Machine Design
Creo offers a powerful yet flexible solution that grows with your design needs. From concept to production, Creo’s advanced tools and workflows enhance design efficiency. Designers can easily adjust, optimize, and validate models, to achieve an accurate result. No matter what industry or purpose your machine is for, Creo can help you achieve a successful product. To learn more about PTC Creo, contact our experts today.