The medical device industry is one of the most regulated industries due to the importance of the products they manufacture. Efficiently producing high-quality products that comply with regulatory standards is the key to successful medical device manufacturing. Implementing a seamless digital thread can help achieve this outcome. Utilizing PTC products, medical device manufacturers can connect design, manufacturing, and service teams. Let’s explore how leveraging the digital thread with PTC can help medical device companies remain competitive and compliant.
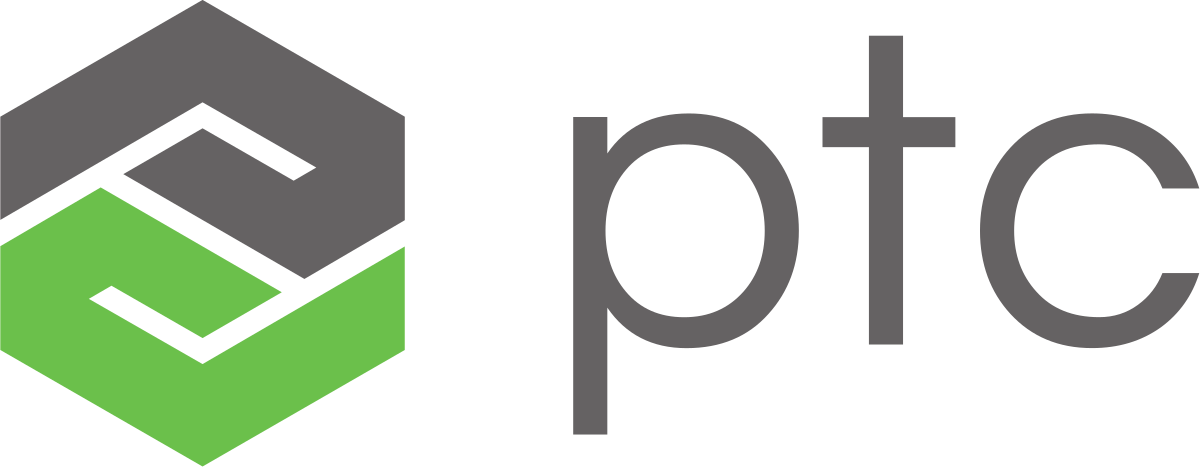
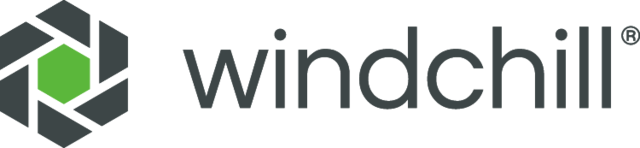
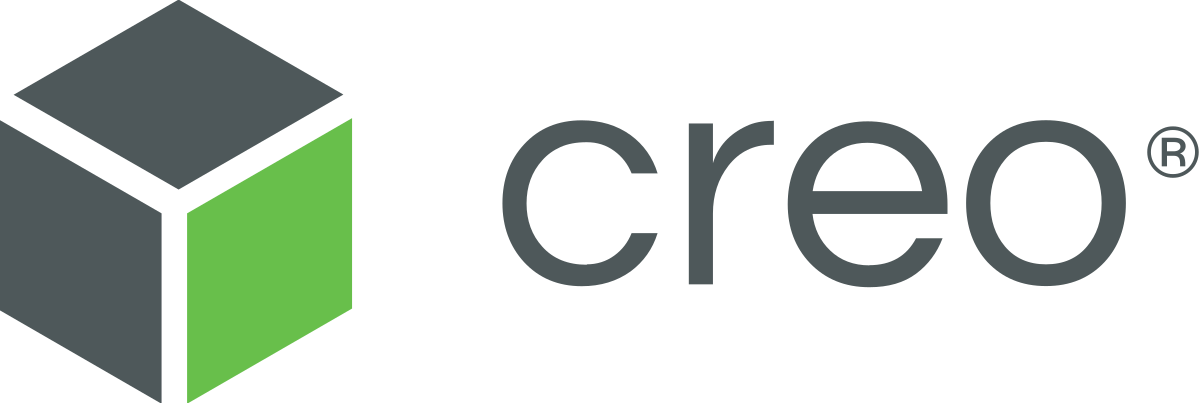
Getting Your Digital House in Order with Creo and Windchill
The first step in implementing the digital thread is to get your digital house in order. Integrating PTC’s CAD tool, Creo with its PLM solution, Windchill creates a model-based digital thread. Integrating these tools allows users to automate processes and better collaborate to maintain compliance with ever-changing regulations. More specifically, it allows companies to streamline product development by ensuring all teams are working from the same set of data. Ensuring consistency reduces errors in design and documentation which is vital to successful production. Overall, this integration leads to reduced risks, a faster time-to-market, improved traceability, and lower costs.
Optimizing Service Operations
When implementing your digital thread, it is critical to optimize your service operations. Connecting people, parts, and information through a digitized service foundation allows manufacturers to efficiently manage operations. This ensures medical devices are properly maintained, meaning they function safely, efficiently, and in compliance with regulatory standards throughout their lifecycles. Oftentimes, current systems lack the ability to provide actionable data for service teams, which creates bottlenecks in delivering timely and effective support. A digitally connected service foundation helps quickly fulfill customer needs by increasing traceability and lowering service cycle times.
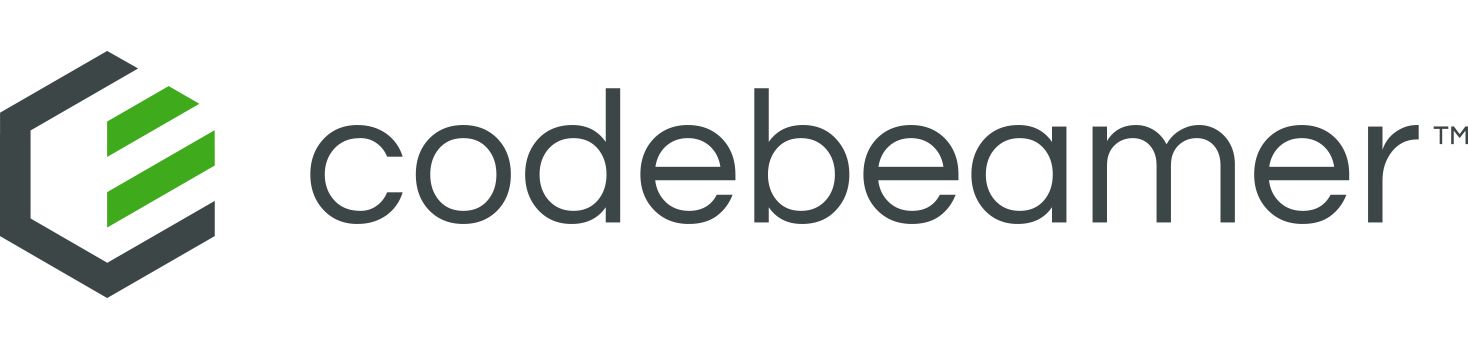
Requirements Management and Software Development with Codebeamer
As software continues to play an increasingly important role in medical device manufacturing, adopting agile development practices is essential. These practices promote adaptability and continuous improvement in the development process. Software as a Medical Device (SaMD) use is also increasing, with software diagnosing diseases and aiding in treatment decisions. With this have come stricter cybersecurity requirements. PTC’s ALM tool, Codebeamer helps medical device companies modernize their requirements management to adapt to new requirements. Codebeamer provides full traceability of user needs and validated products as well as offering early risk management. This leads to faster innovation cycles, helping organizations remain compliant with new standards.
Digital Workflows in The Digital Thread
Transforming paper-based processes into digital workflows is important in most industries, but specifically for medical device manufacturers. Compliance and precision are especially important. By empowering frontline workers with digital tools, companies can enhance their productivity and maintain compliance with Standard Operating Procedures (SOPs). This digitization allows companies to reduce errors and easily onboard new employees to help alleviate the shortage of skilled workers.
Maintaining a Consistent Supply of Medical Devices with Windchill
In addition to digitization, maintaining a consistent supply of life-saving devices is a large part of medical device manufacturing. This maintenance requires a digital infrastructure that connects engineering, manufacturing, and operations. The digital thread, more specifically the integration of Windchill PLM and IoT solutions, allows medical device manufacturers to ensure the timely delivery of high-quality products. Ensuring this continuous product flow is critical for maintaining patient care.
Pharmaceutical Solutions with ThingWorx DPM
In the pharmaceutical industry, utilizing transformational manufacturing solutions can maintain the flow of life-saving drugs and medications to providers and patients. These solutions enhance efficiency, productivity, and quality by leveraging IoT. These IoT solutions are powered by PTC’s ThingWorx DPM. This platform helps increase data transparency for production steering, improve product quality, and reduce energy costs.
Utilizing Connections in The Digital Thread
Once your digital thread is set up, you can strengthen it by connecting engineering with service execution. PTC users can leverage their existing Windchill installation to extend the digital thread from engineering across manufacturing to service. Furthermore, users can also connect medical products by leveraging ThingWorx. Smart connected medical devices integrate with digital technologies, enabling real-time data collection, analysis, and communication. These connections lead to quicker resolution times for failures and better data-driven decisions made.
Ready to Strengthen Your Digital Thread with PTC Solutions?
In today’s medical device landscape, the digital thread is a game changer. By integrating PTC solutions like Creo, Windchill, Codebeamer, and ThingWorx, Medical and Pharmaceutical companies can streamline development, improve regulatory compliance, and ultimately deliver better outcomes for their patients. If you have questions or would like to implement the digital thread, contact us today.