In industries where innovation and time-to-market define competitive success, effective change management is critical. Utilizing the proper tools to manage these changes is vital. Two industry leaders—Vaillant Group and Kirloskar Oil Engines Limited (KOEL)—have transformed their change management processes using PTC Windchill. By automating and optimizing workflows, these companies have reduced rework and increased efficiency. Let’s explore how Windchill’s capabilities aided in this process.
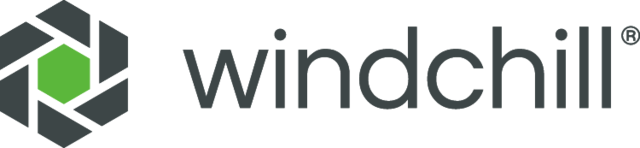
How Windchill Streamlined Change Management Across a Global Enterprise
With over 140 years of history, Vaillant Group is a global leader in heating, ventilation, and air-conditioning technology. Despite this experience, their reliance on manual processes created significant inefficiencies. They were manually entering Engineering Change Notices (ECNs) through spreadsheets and emails. Additionally, they lacked system-controlled workflows, traceability, and access controls. These inefficiencies led to high levels of rework due to error-prone manual data entry. Lastly, they had fragmented integration between their CAD, PLM, and ERP systems. In other words, no proper digital thread. These inefficiencies led to long lead times, poor traceability, and increased rework. Overall it delayed their time-to-market and raised costs.
Windchill for Vaillant
In order to modernize its change management processes, Vaillant adopted Windchill PLM. They performed their digital transformation in phases. Phase one introduced workflow-controlled creation of parts and BOMs. It also automatically transferred data between Windchill and SAP. Phase two added advanced PLM functionalities to manage requirements, product compliance, and cost tracking. Phase three used IoT data to predict failures, optimized designs based on field feedback, and integrated AR for service delivery.
The Results of Streamlining Change Management with Windchill
After implementing Windchill, Vaillant achieved significant efficiency improvements. They had a 40% decrease in master data rework. Additionally, they had a 48% reduction in follow-up documentation. Lastly, their ECN processing time became 25% faster. By using Windchill to eliminate manual errors, automate workflows, and connect systems, Vaillant accelerated their product lifecycle and improved overall quality.
Transforming Service-Centric Delivery with Windchill PLM
KOEL had a similar experience to Vaillant prior to using Windchill PLM. KOEL is a market leader in diesel engine manufacturing that faced difficulties managing its vast product data repository. It has over 1,000 equipment models, 10,000 parts lists, and 12,000 interactive illustrations. Its employees and stakeholders were depending on outdated, static 2D catalogs for service parts which led to delays and errors. This inefficient parts and change management process needed a revamp. KOEL needed a modernized system to manage changes and deliver accurate, up-to-date information to their dealers and service teams. This would help them deliver customer satisfaction.
Windchill for KOEL
KOEL partnered with PTC to implement an enterprise-wide PLM foundation integrated with PTC’s Arbortext Content Delivery (ACD). This transformation involved moving to a single source of truth for product and service data. Additionally, it digitized the service parts catalog with 3D interactive illustrations linked to CAD models. All of this made visualizing much quicker and easier for stakeholders. In addition to this, PTC automated all change management processes with up-to-date SBOMs derived from upstream EBOMs.
The Results of Implementing Enterprise-Wide PLM with PTC Windchill
These new additions to KOEL’s workflows realized substantial efficiency gains. They had a 10% reduction in late-stage engineering changes. Additionally, they had 73% fewer production-related changes. Lastly, they had a 25% reduction in product codes and new parts creation. Overall, the new system improved technician effectiveness, reduced service errors, and enhanced customer satisfaction by enabling faster, more accurate responses to service needs.
How Windchill Transforms Change Management
Both Vaillant Group and KOEL demonstrate the transformative power of Windchill PLM in overcoming the following change management challenges:
- Errors and Rework:
- Manual tracking systems were replaced with automated workflows, significantly reducing rework and documentation follow-ups.
- Inefficiencies:
- Seamless integration between PLM, CAD, and ERP systems provided a unified data source, eliminating silos and manual data entry errors.
- Poor Collaboration:
- With access to up-to-date product data and service parts information, cross-functional teams collaborated more effectively, reducing delays and errors.
- Unsatisfied Customers:
-
- Enhanced service delivery through accurate, accessible data ensured better customer experiences which is crucial for retaining market leadership.
Ready to Successfully Manage Changes with Windchill?
PTC’s Windchill PLM has proven to be a critical enabler for companies like Vaillant and KOEL. The results of double-digit efficiency improvements in change management speak for themselves. These companies have achieved faster time-to-market, reduced costs, and improved product quality through automating workflows and integrating systems. If your organization is ready to realize similar benefits, consider implementing Windchill PLM. Contact our experts today to learn how we can help you harness the power of digital transformation to achieve your goals.